Advancing waste heat recovery solutions in industrial operations
- Jamie Zachary
- Feb 26
- 2 min read
Updated: Apr 4
Econotherm-Schuylkill collaboration featured in Process Industry Informer
With increasing emphasis on corporate environmental responsibility, industrial operators across various industries are re-exploring opportunities to repurpose otherwise-wasted heat. When implemented effectively, the benefits have shown to be significant, ranging from a reduction in primary energy inputs to fewer greenhouse gas emissions.
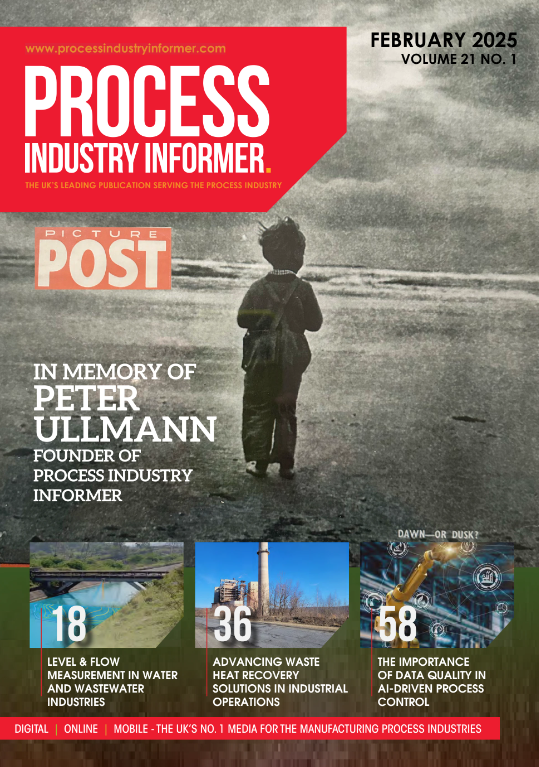
In the case of Schuylkill Energy Resources (SER), the U.S.-based independent power producer had started down this road long ago. The company had been operating a Q-Dot heat pipe air pre-heater (APH) at its 80-MW St. Nicholas Electric Power Generation Station in Shenandoah, Pennsylvania, U.S. since 1987.
Yet over the decades, the performance of the heat pipe APH had degraded due to several known issues, including pipe corrosion, leakage, degradation of the organic working fluids. So, SER turned to Econotherm, whose collaboration on a solution for the power producer has now been featured in the February 2025 issue of Process Industry Informer.
From Process Industry Informer: "Initially, the scope of the repairs was to address only the primary air heater. However, the product manufacturer had discontinued support on Q-Dot heat pipe APH, so SER contacted Econotherm, a UK-based company that specializes in the design and manufacturing of industrial waste heat recovery heat exchangers based on heat pipe technology."
Some highlights of the savings that Econotherm helped SER realize through a modernization of the Q-Dot unit:
Reduction of 57.4 million BTU or 2.9 coal short tonnes per hour burned.
Hourly savings of $173.23 USD based on price per tonne of $187.70/hour coal price based on MMBTU coal.
Annual savings of $1.5 million.
Reduction of 42,959 tonnes of carbon dioxide per annum.
Substantial reduction in quench water consumed at the power station
Access the full article here.
Comments